Bethlehem Steel Shipyard
Bethlehem Shipbuilding Corporation, or BethShip as it was commonly called, owned 15 shipyards during World War II. At its peak during World War II, Bethlehem Shipbuilding was the most profitable of all the shipyards in the country.
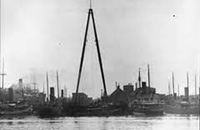
Bethlehem Shipbuilding began with facilities around the U.S.
The yards at Staten Island and San Pedro built destroyers. Staten Island also had a foundry that made propellers for Bethlehem’s other facilities.
Armstrong, Ruberoid, Pittsburgh Corning and Johns-Mansville were familiar to the shipyard workers. These were the manufacturers that provided the asbestos-containing products used to construct warships. But the material’s use wasn’t only confined to shipbuilding. Asbestos lagging in the form of pipe insulation, block and cement was used throughout these shipyards.
Exposure to these products caused many shipyard workers to develop asbestos-related diseases.
A 2017 article reported on shipyard employees with a history of moderate asbestos exposure. They are almost four times more likely to die of mesothelioma.
Multiple Uses for Asbestos Products
A walking tour of a typical Bethlehem facility would reveal just how many uses there were for asbestos. Raybestos cloth was stored and dispensed in the yard storeroom. The large rolls of asbestos fabric and insulation wrapping were cut to order depending upon need, and that would release fibers into the air, continually exposing the employee who managed the storeroom to dangerous dust.
Workers in the Y department cleaned up asbestos materials, including blankets, left by other employees. Rigging department workers like welders and burners constantly used asbestos blankets. Ship fitters always carried a piece of asbestos cloth to kneel down on while working on the hot steel decks. But that wasn’t their only exposure, because these tradesmen worked alongside welders and burners who also used asbestos fabrics and other asbestos-contaminated materials such as gaskets.
Workers in the boiler room, engine room and pump room (who also worked with asbestos insulation) tore off and replaced asbestos cloth, in many cases with their bare hands, causing a windfall of fibers to be released into the air. Using asbestos cloth was a way of life in the 1940s at Bethlehem Shipyards; they even went so far as to use it to patch torn work clothes.
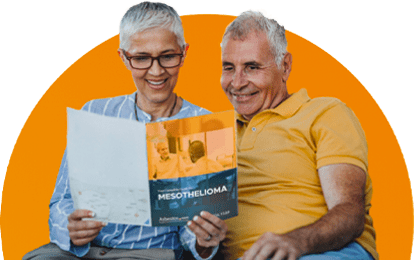
Learn about your diagnosis, top doctors and how to pay for treatment.
Get Your Free GuideOutside Contractors also Installed Asbestos
In addition to the asbestos materials used and cut onsite, Bethlehem shipyards also employed outside contractors to supply and install the toxic materials. One such supplier was the McCormick Asbestos Company, who not only sold the product, but sent its own employees to install asbestos-containing insulation, block and cement.
Safety Standards were not Enforced at Bethlehem
In 1943, a set of rules called “The Minimum Requirements for Safety and Industrial Health in Contract Shipyards” was made. People in charge of the Navy and ships agreed on these rules. Navy leaders explained how to follow the rules. They sent this book to all shipyards that worked with the Navy.
The rules talked about using safety. They said when to use special masks and fans to keep the air safe. But when they checked at Bethlehem, they saw that nothing changed. The Navy tried to make things safer, but people still didn’t follow the rules about asbestos.
Recommended Reading